Maximize Manufacturing Efficiency with a Powerful ERP System

The constantly changing manufacturing environment requires more than just traditional management tools to stay ahead of the competition. This is where Enterprise Resource Planning (ERP) systems come in as a game-changer. It integrates every aspect of manufacturing, from inventory and supply chain management to customer relations and financial operations.
ERP for manufacturing goes much beyond just being a software—it is a comprehensive solution that is designed to streamline workflows, enhance decision-making, and provide real-time insights. In this blog we will explore how modern ERP solutions are driving efficiency and innovation in the manufacturing sector, and how it can help your business to reach its full potential.
What is ERP in Manufacturing?
Enterprise Resource Planning (ERP) systems are interoperable information systems that allow managers to efficiently process, manage, and execute several business activities. On the one hand ERP for manufacturing is a piece of software, on the other hand it is an operational management tool which integrates all the production and operational activities from shop to doorstep.
The history of evolution of ERP software in manufacturing began with the development of Material Requirements Planning (MRP) systems which were in existence in the 1960s with an emphasis on inventory management and planning. The logical evolution of MRP progressed into MRP II by the late 1970s whereby additional features such as demand forecast as well as capacity planning were added. In the late 1980s and early 1990s, ERP commenced wherein MRP gained additional functions in other business areas, most notably finance, human resources, and customer relations. With it came a series of modern ERP systems that formed the cornerstone of enterprise resource management with effective control and interconnection of various processes and data in the organization.
ERP software not only helps improve operations but also enhance efficiency and decision-making processes by offering an in-depth view of all factors surrounding the manufacturing process. This balanced approach is quite essential in the present business climates where quick information and rapid responses are the core of obtaining a competitive edge.
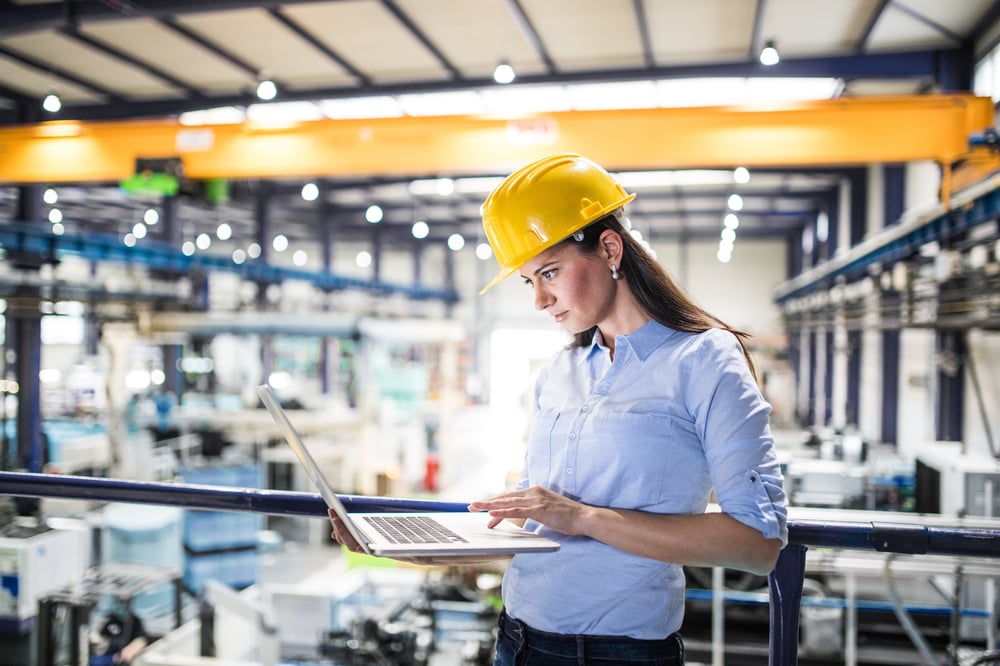















Challenges Faced by Manufacturers
Today’s manufacturers encounter several issues that might affect their efficiency and productivity most notably:
-
Supply Chain Gaps
The challenge of supply chain disruption is regarded as one of the significant challenges in manufacturing fields at present. Geopolitical tensions and wars, natural calamities, pandemics, and other variables can affect lead times as well as the availability of essential materials. Such disruptions not only result in delays in production but also cost overruns and loss of customer confidence.
-
Demand Forecast Errors
Proper inventory decisions such as purchasing or stocking up on inventory depend on the ability to accurately project demand. Demand forecasting errors can cause serious problems such as overstock, or stock outs which freeze one’s capital, which could have been put in better use. In particular, over-stocking tightens up warehouse space and invites the risk of goods’ obsolescence, while under-stocking could translate into losses through missed sales opportunities and customer dissatisfaction.
-
Product Quality Challenges and Absence of Product Traceability
One of the core principles of any manufacturer is ensuring that locking of quality remains uninterrupted. When quality is not monitored well and there are no quality control measures to trace finished goods, defective products may be released in the market leading to customer dissatisfaction, and in some cases, health hazards. Further, in the absence of appropriate quality assurance systems, it is difficult to identify the cause of these quality problems making it even harder to devise strategies that will enhance the processes and avoid similar problems in the future.
-
High Production Costs
Unpredictable prices of raw materials and a high operational cost can severely impact a manufacturer’s costs. Assigning a budget and setting a price rate are difficult due to price fluctuations on commodities, impacting the profitability. Additionally, manufacturers have to constantly find new ways to improve efficiency levels and cut down on wastage as overhead costs like power, labor and maintenance are quite high.
-
Regulatory Compliance
Manufacturing activities are often associated with a multitude of rules and regulations governed by specific industries. The nature of these compliance standards which tend to change from time to time means that manufacturers will always be on their toes in order to meet the regulatory requirements. The violation of such provisions leads to penalties, lawsuits, and loss of goodwill for the organization.
-
Disparate Systems and Data Silos
Another common issue faced by many manufacturing environments is the deployment of separate systems and isolated data that hamper effective communication. This lack of synergy can lead to inefficiencies, errors, and missed opportunities for optimization. When information is not shared easily across functions, the entire manufacturing process can be slowed down, affecting service levels and customer satisfaction.
Key Features and Functionality of Manufacturing ERP
Manufacturing ERP comes equipped to face all the challenges that have been enlisted above with some key functionalities such as:
-
Inventory Management
The manufacturing ERP software improves on the traditional ERPs by controlling stock management that cuts back operational investments while efficiently responding to customer’s needs. There are such tools as JIT (Just-In-Time) Inventory which helps reduce overstocking or stockouts, maintaining accurate inventory levels. ERP software also improves supply chain management functions by taking care of supplier coordination, logistics and improving the flow of goods from raw materials to finished products.
-
Production Planning and Scheduling
An ERP system improves on the software application production planning and scheduling so that there is proper utilization of the resources available, thereby meeting the production requirement. Capacity planning tools analyze and match production capacity to shifting demands, in order to optimize resources. Allocation of resources is done via real-time insights of available resources and materials. In addition, real-time production monitoring helps identify and address holdups, track productivity, and adjust operations dynamically.
-
Quality Management
Quality management plays a key role in any ERP system making sure customers are happy and products meet high standards. These systems use tough quality checks during manufacturing to hit set benchmarks. They also have features to check if rules like ISO and FDA standards are being followed, which keeps product quality steady. By spotting and fixing possible problems manufacturing ERP helps cut waste and improve overall product quality.
-
Shop Floor Control
Manufacturing ERP gives useful tools to better control the shop floor in tricky and changing production settings. Work order management keeps an eye on each part of the production process from start to end, while machine checks make sure upkeep happens on time to avoid shutdowns. Labor tracking helps put workers where they're needed most using people in the best way to keep boosting how much gets made.
-
Integration with IoT and Industry 4.0 Technologies
The combination of ERP systems with IoT and Industry 4.0 tech is causing a revolution in how factories work making operations smarter. When IoT devices feed sensor data into the system, it gives a clear picture of how well machines are running and what's happening on the factory floor. By looking at this data, companies can guess when equipment might break down and fix it before it does, which means less time wasted on unexpected repairs. AI and machine learning make all of this even better doing tasks automatically so people don't have to step in as much.
-
Regulatory Compliance
ERP software plays a key role in helping manufacturers meet tough regulatory compliance rules. It aids in sticking to industry norms and handling certification steps for rules like ISO and FDA. This feature makes sure manufacturers always follow legal standards keeping product quality and safety high. Also, ERP for manufacturing helps track regulations keeping the system up-to-date with the newest rule changes, and adding these into production processes to ensure ongoing compliance. This non-stop following of rules is crucial for manufacturers to dodge fines and keep their operations legal.
Benefits of ERP Adoption in Manufacturing
The adoption of ERP for manufacturing brings about transformative benefits such as:
Improved Operational Efficiency
-
Streamlined Workflows
Manufacturing ERP streamlines various activities by automating routine processes and ensuring consistency in various organizational departments and activities. This helps minimize the human efforts and time taken in rendering various tasks. -
Reduced Lead Times
Effective control of production planning and materials acquisition through the help of ERP programs help reduce the time needed for order fulfillment and delivery. -
Minimized Waste
ERP solutions help in timely production planning and inventory management which leads to reduction in case of overproduction, minimizing material waste, and lowering the cost of holding excess inventory.
Enhanced Visibility and Control
-
Real-Time Data Insights
SAP ERP for manufacturing provides real-time data for the entire manufacturing process, from the shop floor to finance teams, helping managers to make informed decisions swiftly. -
Better Decision-Making
ERP systems’ analytical tools effectively examine organizational processes, helping the company make relevant strategic decisions. -
Proactive Problem-Solving
ERP software helps in the early detection of issues that are likely to cause concern hence enabling management to have a chance to counter any problems that are likely to occur in the future.
Cost Reduction
-
Lower Inventory Carrying Costs
Advanced solutions of ERP practices assist in controlling the inventory and avoid inefficiencies related with excessive products and storage costs. -
Optimized Resource Utilization
ERP systems increase effectiveness of resources management for utilization of resources thereby decreasing operational expenses. -
Reduced Overhead Expenses
Since ERP software integrates most if not all the core business functions, it reduces the number of times people have to get involved, thus reducing labor cost and overheads.
Increased Agility and Responsiveness
-
Adaptation to Market Demands
Compared to typical client-server architectures, ERP systems have the capability to provide the human resources and remunerations quickly in response to market dynamic or changing customer demands. -
Scalability
The manufacturing ERP is usually developed to expand with the manufacturing company since it can adapt to the new internal processes, products, or places without affecting the business process. -
Flexibility in Production Processes
When it comes to ERP, manufacturers are able to bring various product changes or even create a completely new line of products to follow the changing demand.
Compliance and Risk Mitigation
-
Adherence to Regulatory Requirements
ERP systems assist in the adherence to local and international laws and regulation. This being the case, ERP solutions provide extensive coverage when it comes to tracking, and they also record product histories and every activity done in the entire business.
Competitive Advantage
-
Innovation
ERP systems help R&D and Product development activities which makes implementing innovative products much easier. -
Customer Satisfaction
Since on-time delivery and service is faster and product quality is better, ERP solutions provide the competitive edge of establishing a reasonable reputation and increased customers’ loyalty.
Selection of ERP Solutions
When selecting an ERP system, manufacturers should consider:
-
Scalability
It is expected that the system should be scalable so that it can expand as the business expands. It should be able to cater to other processes, and a larger number of users without compromising performance. -
Customization
Every production process is different, and the ERP system should be able to accommodate certain requirements. -
Integration Capabilities
The solutions in the ERP for manufacturing should be compatible with other applications like CRM, MES as well as SCM. -
Mobile Access and Cloud Deployment
Today’s ERP systems can be delivered through the cloud and increasingly allow users access from mobile devices. -
Data Analytics and Reporting
In order to get good value from large amounts of data, strong analytical and reporting tools are necessary. -
Quality of Onboarding and Support
A reliable ERP partner should provide thorough onboarding and continuous support to ensure smooth operation and adaptation.
Also read: Driving Mid-Sized Manufacturing Enterprises Success with Custom ERP Systems
Case Studies and Success Stories
As we delve into the tangible impacts of ERP systems, it is essential to understand how they transform theoretical benefits into real-world successes.
Eagle Cement, a prominent cement manufacturer established in 1994, faced operational challenges with increased production volumes. Struggling with inefficient systems, non-standardized material coding, and workforce resistance to technology, Eagle Cement opted for Ramco's ERP system due to its cost-effectiveness and SaaS model. The Ramco deployment was swiftly completed, successfully integrating processes across sales, production, inventory, finance, and costing. This ERP implementation enabled real-time operations tracking and streamlined decision-making, significantly reducing costs with its cloud-based solution. The solution was implemented during the COVID-19 pandemic completely virtually by a team of 10+ Ramco consultants with Ramco providing extensive training to 30+ Eagle Cement users on the ingenious solution. The successful deployment of Ramco's ERP not only optimized operations but also equipped Eagle Cement for national expansion, maintaining its commitment to quality and innovation
Another leading Indian manufacturer of automotive components specializing in tapered and parabolic springs faced significant challenges due to a weak macroeconomic environment, including subdued demand and increased costs from stricter emission standards. These challenges were compounded by internal inefficiencies such as poor stock visibility and reliance on disconnected, manual systems. In response, the company partnered with Ramco to implement a comprehensive ERP solution that unified production, inventory management, maintenance, procurement, sales, distribution, and after-sales into a single system, significantly enhancing operational visibility and efficiency. The ERP implementation resulted in a 90% reduction in processing times, increased sales force efficiency by reducing manual tasks, transitioned to paperless operations, and improved financial reconciliation, ultimately boosting overall profitability. This transformative outcome not only streamlined operations but also set a new industry standard for operational excellence, leading to the solution's expansion across more plants, and showcasing the profound impact of advanced ERP solutions in driving business growth and efficiency.
ERP Implementation and Optimization in Manufacturing: Best Practices
-
Pre-Implementation Planning
Pre-implementation planning for an ERP system requires an analysis as to what the company operationally lacks and where those painful operational points are. With insights from as many business areas they have so that departments can share their specific set of requirements. The sooner that you involve your key stakeholders across the multiple departments, the better off you'll be in outlining those requirements and understanding what their initial challenges might look like. Finally, choosing the best ERP solution for your company should also be determined by industry specific functionality, scalability & usability with ease of integration supporting existing systems to suit most business needs.
-
Implementation Methodology
A successful ERP system needs a phased rollout: you can gradually step into daily operations and subsequent adoption, based on the feedback of first early users before going live. This is also critical for a successful transition to an ERP and must clearly communicate the benefits of the new system, address concerns and set expectations as part of a comprehensive change management strategy. You should ensure that proper training and support are provided once the system is implemented, so it will be easier for users to get used to new changes included in an update.
-
Migrate and Integrate all your Data
Migrating your data will require cleaning obsolete or redundant data and fixing any inconsistencies. In addition, data mapping becomes crucial to list down how the transfer would take place from existing systems to the new ERP and ensure all important information is accounted for at right places. Integration with existing systems, such as CRM, SCM, or HRM, is also vital to ensure seamless integration, maintaining data continuity and workflow efficiency across the organization.
-
Continuous Improvement
In order to improve the performance of an ERP system, regular measurement must be conducted in various facets with strategic metrics at a given interval on how well it performs against the company goals. Further, feedback loops should be established to let users give an understanding of the functioning of the system and its usability-insights so valuable for continuous improvement. Also, leveraging the collected feedback and performance data, iterative optimization should be performed to refine and adjust the ERP system, including workflows, interfaces, and functionalities, to increasingly meet organizational needs and enhance user experiences.
-
Factors to Consider for Vendor Selection
The implementation of ERP in manufacturing must be accompanied by a proper selection process of the vendors. A rating of a vendor has to be based on previous experiences in similar industries and their reputation for offering support services to their customers. The selection process should ensure that the ERP software being provided by the selected vendor matches the exact needs identified at the earlier stage, paying much attention to flexibility and customization options. Finally, while negotiating the contract, secure favorable contract terms about support and maintenance, customization options, and scalability to accommodate the growing needs of the future.
-
Post-Implementation Support
For effective ERP system management, regular maintenance is essential to ensure it operates efficiently and remains secure. You should regularly plan for and perform upgrades to take advantage of improved features or technologies to enhance performance and user experience. Create a continued support system that helps consumers with the tech issues or questions related to ERP solutions. This support can either be internal or by the vendors as per availability of expertise to provide all time accessible, dependable help for system users.
Future Trends and Innovations in Manufacturing ERP
The Manufacturing ERP landscape keeps changing and is poised to do so for as long as technology continues to evolve, and the market continues to swing. The future may hold a number of trends that include:
-
Advanced Analytics and Predictive Modeling
Advanced analytics in ERP systems revolutionizes demand forecasting by using historical data and market trends to estimate future demands with a high degree of accuracy. Similarly, predictive maintenance in such systems also foretells possible equipment failures for proactive maintenance that ensures minimal downtime and prolongs the life of equipment for overall enhanced operational efficiency .
-
Cloud-based ERP Solutions and SaaS Models
The cloud-based ERP solution has unrivaled accessibility of data from any location, which is in very high demand from companies with multiple locations or a remote workforce. An ERP SaaS model reduces upfront costs by subscription, inclusive of ongoing support, update, and maintenance, thereby shifting IT expenditures to a more predictable operational cost.
-
Adoption of AI and ML in Manufacturing
Artificial Intelligence (AI) and Machine Learning (ML) are increasingly integrated into ERP systems to optimize manufacturing processes and automate routine tasks. These technologies analyze large datasets to identify inefficiencies and automate mundane tasks, thereby enhancing productivity and reducing waste while improving employee satisfaction by allowing them to focus on more complex activities.
-
Expansion of IoT and Smart Device Connectivity
IoT integration with ERP systems enables real-time monitoring and control over all aspects of manufacturing. This connectivity provides immediate insights into operations, allowing for dynamic adjustments in inventory management and production processes. Smart devices and sensors collect detailed data at every manufacturing stage, enhancing the depth of operational understanding and supporting data-driven decision-making.
-
Blockchain Technology for Enhanced Transparency
Blockchain technology brings a new level of transparency and traceability to supply chains, crucial in industries that value authenticity such as pharmaceuticals and luxury goods. It creates immutable records of transactions and product movements, enhancing product traceability from production to delivery, which is essential for quality control and managing recalls efficiently.
-
Integration with AR and VR
Augmented Reality (AR) and Virtual Reality (VR) are reshaping training and operational procedures in manufacturing. These technologies provide immersive training simulations and enhance visualization of complex data and operational workflows. For example, AR can overlay maintenance data directly onto equipment, helping technicians to quickly identify and address issues, thus reducing downtime and improving operational efficiency.
Conclusion
Manufacturing today is inundated with data from various sources including production equipment, supply chain activities, and market interactions. The challenge lies not just in capturing this vast amount of data, but in effectively analyzing and utilizing it to make strategic and operational decisions. In the fast-evolving landscape of manufacturing, the ability to make quick, informed decisions is a critical competitive advantage. ERP software, with its comprehensive integration and data management capabilities, has become an indispensable backbone for modern manufacturing operations. The transition towards data-driven decision-making facilitated by ERP systems is not merely a trend but a fundamental shift in how manufacturers operate and thrive in an increasingly complex and volatile market environment.
Also read: Why Digital Transformation Is Needed In The Auto Ancillaries Industry
You May Also Like!

