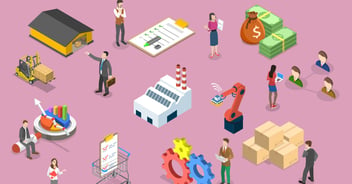
How Textile ERP Weaves Efficiency in Yarn Manufacturing
Published :
The path from cotton fields to finished yarn is a global ballet of precision—where procurement, quality checks, and inventory management must align seamlessly across continents. With fluctuating cotton quality, stringent standards, and logistical hurdles, even minor disruptions ripple through production. Manual processes strain efficiency, while real-time visibility remains elusive. This is where digital textile ERP steps in—turning fragmented operations into a synchronized, data-driven supply chain that ensures quality, minimizes waste, and keeps production flowing smoothly.
The cotton-to-yarn supply chain is a complex ecosystem where multiple variables must align for smooth operations. However, several persistent challenges make this alignment difficult.
Addressing these challenges requires robust planning, real-time data analytics, strong supplier relationships, and contingency strategies. While the road is not easy, a robust textile ERP solution can help mitigate risks and ensure a resilient supply chain.
Running a cotton-to-yarn business involves juggling multiple processes—procurement, quality control, production, and asset management—all while maintaining efficiency and profitability. This is where ERP systems become indispensable.
An ERP integrates core business functions into a unified platform, providing real-time visibility and control. For cotton-to-yarn manufacturers, this means:
The journey from cotton bales to high-quality yarn is a complex, multi-stage process where precision and coordination are critical. Any disruption—whether in procurement, quality checks, or spinning—can halt production, leading to costly delays and rework. Digitalizing this process with a textile ERP system ensures seamless operations, real-time monitoring, and data-driven decision-making, minimizing risks and maximizing efficiency.
ERP systems digitize every step, from procurement to yarn conversion. When cotton bales arrive, real-time data capture records weight, moisture content, and fiber quality, ensuring only compliant materials proceed. Automated quality checks eliminate human error, flagging deviations before they disrupt production. For instance, excess moisture can weaken fibers, while inconsistent weight affects yarn uniformity—textile ERP prevents such issues by enforcing strict quality thresholds.
Procurement becomes faster and more transparent with ERP. Payments are automatically processed based on accepted quantities, reducing disputes and delays. Suppliers receive instant updates, fostering trust and long-term partnerships.
The cotton-to-yarn workflow involves:
If a defective bale slips through or a machine malfunctions, the entire line may stop, forcing reprocessing. Textile ERP tracks each batch digitally, ensuring traceability and quick issue resolution. For example, if a moisture imbalance is detected in spinning, the system traces it back to the source, preventing further waste.
By digitizing workflows, ERP minimizes manual intervention, reduces downtime, and optimizes inventory. By automating quality checks, they reduce material waste and rework costs. Maintaining the right cotton inventory while meeting yarn demand is a delicate balance. Textile ERP transforms this challenge by tracking stock in real time, forecasting demand accurately, and optimizing production schedules. Real-time inventory tracking prevents overstocking and shortages, optimizing working capital. Production scheduling becomes precise, minimizing machine downtime and energy waste. Digital procurement ensures fair cotton pricing, while automated payments accelerate cash flow. In short, data-driven insights enable mills to achieve higher output with fewer resources.
A leading South Indian yarn manufacturer partnered with us to streamline their operations using ERP. The results were remarkable: 5% higher asset utilization and productivity, and significant improvement in quality deviation through timely alerts. By digitizing workflows, they gained precision in monitoring and faster response times—proving that smart technology drives tangible growth. Their success showcases how Ramco ERP turns operational challenges into measurable gains.
The cotton-to-yarn journey demands precision, agility, and end-to-end visibility—all of which modern ERP systems deliver. From automating quality checks and optimizing inventory to preventing costly disruptions, textile ERP empowers textile manufacturers to transform supply chain challenges into competitive advantages. The proven results—higher productivity, fewer errors, and stronger supplier relationships—speak for themselves. In an industry where margins are tight and efficiency is everything, adopting ERP isn’t just an upgrade; it’s a strategic necessity.
Ready to future-proof your operations? The time to digitize is now. Explore how Ramco ERP can streamline your cotton-to-yarn business—connect with us today.
All Rights Reserved. © Copyright 2024. Ramco Systems.