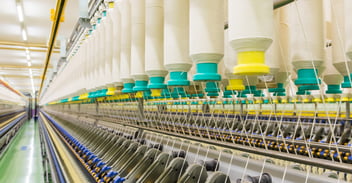
Textile ERP: Enhancing Quality Control and Assurance in Textile Production
Published :
In the competitive textile industry, maintaining consistent product quality is paramount for success. Quality Control (QC) and Quality Assurance (QA) play crucial roles in ensuring that products meet customer expectations, comply with industry standards, and maintain brand reputation. This blog explores the fundamental concepts of QC and QA in textile production, examines the common challenges faced by manufacturers, and delves into the role of textile ERP systems in enhancing quality management.
Quality Control (QC) and Quality Assurance (QA) are essential practices in textile production, ensuring that products meet specified standards and customer expectations. QC focuses on detecting and addressing defects during production through inspection and testing. QA emphasizes systematic planning and process optimization to prevent defects from occurring. Together, they form a comprehensive framework to deliver consistent quality throughout the textile supply chain.
Common quality issues in textile production that make QC measures a necessity include:
Effective QC and QA systems are crucial for minimizing these costs and maintaining customer satisfaction in the competitive textile industry.
Textile production often involves supply chains spread across multiple regions, with stages like yarn manufacturing, dyeing, and assembly outsourced to different vendors. While cost-effective, this fragmentation complicates quality management due to communication gaps, varying standards, and limited visibility, leading to delays, defects, and financial losses.
Inconsistent raw material quality, such as variations in fiber strength or colorfastness, directly impacts the final product. These issues arise from supplier limitations in resources or quality checks. Managing multiple suppliers with differing standards makes it challenging to ensure uniform material quality.
Manual inspections dominate textile quality control, but they are prone to human error due to fatigue, subjective judgment, and time constraints. This labor-intensive method often misses subtle defects, causing inefficiencies and reducing overall accuracy in identifying flaws.
Textile manufacturers must meet diverse global standards like ISO 9001 and OEKO-TEX, which ensure product safety and sustainability. However, keeping up with evolving regulations, conducting audits, and training staff requires significant effort. Non-compliance risks fines, legal issues, and restricted market access.
In essence, ERP solutions act as the backbone of a modern textile manufacturing operation, empowering businesses to improve quality control, enhance efficiency, and gain a competitive edge in the market.
These modules of a textile ERP automate various aspects of the inspection process, significantly improving efficiency and accuracy. For example, imagine a garment manufacturer using a textile ERP system with integrated image recognition technology. This system can automatically analyze images of finished garments, identifying defects such as misaligned seams, missing buttons, or color inconsistencies. This automation reduces the reliance on manual inspections, which can be time-consuming and prone to human error. By quickly identifying and addressing defects, manufacturers can minimize rework, reduce waste, and improve overall product quality.
Traceability is crucial in the textile industry, especially for addressing issues like product recalls or ensuring compliance with regulations. Textile ERP systems enable end-to-end tracking of raw materials and finished goods throughout the entire supply chain. For instance, a manufacturer can track a specific batch of cotton from the farm to the finished garment. This traceability allows companies to quickly identify the source of any quality issues, such as contaminated materials or faulty production processes. In the event of a recall, traceability helps to efficiently isolate and contain the affected products, minimizing damage to the brand's reputation. For end-to-end traceability, lot tracking can be an effective method. It helps identify defects, isolate affected batches, and optimize production processes while maintaining compliance with standards like OEKO-TEX® or GOTS.
Maintaining consistent quality standards across multiple production facilities or even across different suppliers can be challenging. Textile ERP systems help to standardize quality protocols by providing a central repository for all quality-related information, including inspection checklists, quality standards, and best practices. This ensures that all stakeholders, from production workers to quality inspectors, adhere to the same quality guidelines. For example, a global apparel brand can use a textile ERP system to ensure that all its manufacturing partners, regardless of their location, follow the same rigorous quality control procedures for dyeing, cutting, and sewing.
ERP systems generate a wealth of data related to production, quality, and supply chain activities. By analyzing this data, manufacturers can gain valuable insights into quality trends, identify potential areas for improvement, and proactively minimize defects. For example, a textile ERP system can analyze historical data on defect rates for different production lines, identify patterns, and predict potential future issues. This allows manufacturers to take corrective actions, such as adjusting production parameters, retraining employees, or addressing supplier performance, before significant quality problems arise.
Implementing a robust QC/QA framework, supported by advanced technologies like textile ERP systems, is vital for the success of any textile manufacturer. By integrating processes, leveraging data analytics, and ensuring compliance with industry standards, businesses can significantly enhance product quality, minimize waste, and improve customer satisfaction. In today's dynamic market, prioritizing quality is not just a competitive advantage, but a necessity for long-term sustainability and growth in the textile industry.
All Rights Reserved. © Copyright 2024. Ramco Systems.