In the RMC industry, every batch is unique, demanding exceptional control across production, delivery, and quality. Meticulously tracking the batches, ensuring end-to-end visibility, and optimizing every aspect of your operations can be complicated. At Ramco, we understand these complexities. With over 60 years of experience in operating RMC plants, we've developed a next-generation ERP solution that addresses your specific needs. Our Ramco ERP for RMC goes beyond traditional software, offering functionalities specifically designed for mix design, asset leasing, dump and divert scenarios, and batch controller integration. Discover how Ramco can help you achieve operational efficiency and profitability.
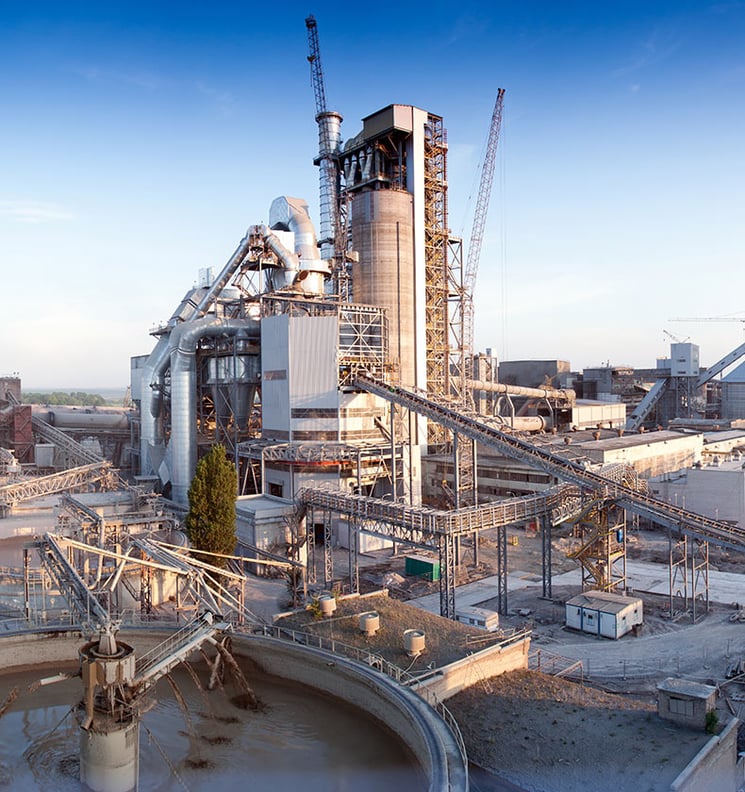
Transforming the RMC value chain
Batching
Precisely blending materials to create uniform concrete mixes.
Real-time operations monitoring
Utilizing technology for instant oversight and optimization.
Demand fulfillment
Strategically meeting customer needs through efficient scheduling and delivery.
Ramco Caters to

Mix design
Ramco ERP supports various concrete mix designs to arrive at your desired grade. The mix design is system-driven, focused on optimizing profitability by incorporating client specifications and even mix designs from RMC companies.

Asset Leasing
We understand that mega projects with mobile on-site batching plants can be complex to handle. Ramco ERP seamlessly manages the batching plant leasing model; wherein clients supply the raw materials, and the RMC company handles the batching process.

Dump and Divert Scenarios
You might encounter scenarios requiring the diversion of transit mixers due to excess loads being ordered by clients, quality restrictions, or grade changes. Ramco ERP helps you divert in-transit mixers from one customer site to another–either full load or partial–based on dynamic business needs.

Batching Controller Integration
Ramco ERP seamlessly integrates with your batching controller system. Once the mix design is finalized, the formula is automatically transferred, allowing for real-time access to material consumption data, and reporting within the ERP. This translates to significant savings.
Ramco has been a partner of Eagle Cement Corporation in its Digital Transformation Journey. Our ERP and HCM implementation, integration and digitalization helps our company improve efficiency, processes, and transparency. Our ERP systems are integrated with other systems like LIMS, Truck scales, RTI Automations, GPS. In addition, our Facial Recognition is integrated with HCM HR System. All this has been made possible by Ramco. Enabling portals for Customers and Vendors help us reach out to them in a digital way providing them transparency and ease of transaction with our company. Mobility solution enabled our users to access the system anywhere on any device, thereby increasing productivity. Dashboards and reports provide holistic visualization of our data in systems that improved visibility and analysis to facilitate timely decision-making.
- Paulo C. Munoz, Head of IT Systems, Eagle Cement
Our Global Customers
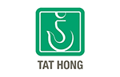
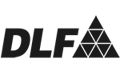
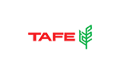

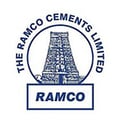
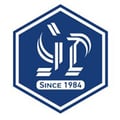

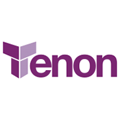
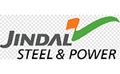
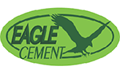
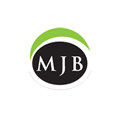
.png?width=805&height=523&name=service-industry-form%20(1).png)
Contact Us for Cement Digital Solutions
FAQs
In the RMC industry, an ERP system is a central hub for concrete production. It manages mix designs, tracks materials, automates reports, and integrates with batching for efficient operations. It simplifies operations and saves money.
RMC businesses need ERP software to juggle complex tasks like mix design, material tracking, and deliveries. It automates processes, ensures accuracy, and provides real-time data for better decision-making, boosting efficiency and profitability. RMC Business has a high volatility in raw material prices. Hence, inventory stocking of raw material is a challenge. ERP can help with precise planning and execution of procurement and operations. In addition, concrete production plan based on site availability and in-transit vehicle availability is a key challenge, which can be overcome by an ERP.
RMC ERP software focuses on concrete production. Key features include mix design creation, real-time inventory management of raw materials, automated batching control, and delivery tracking. This streamlines operations, reduces costs, and ensures quality control for every concrete pour.
RMC ERP software empowers strategic decisions by providing real-time data on costs, materials, and production efficiency. This allows businesses to optimize mix designs, identify cost-saving opportunities, make decisions on customer prioritization and adjust production based on demand, leading to better margins and a competitive edge.
RMC ERP software manages mix design by storing recipes and automating calculations. It then integrates with batching systems for precise production control, ensuring consistent quality concrete and efficient use of materials. The cube combination and quality can be tracked right from production and timely corrective actions can be managed.
Many RMC-specific ERP systems, like the one Ramco offers, can seamlessly integrate with your existing batch controller systems. This allows data exchange for smooth production flow and eliminates manual data entry, saving time and reducing errors.
While ERP systems can't directly calculate NRV, they provide the data you need. They track sales prices and production/selling costs, allowing you to calculate NRV and see if your pricing strategies are on track. Specialized ERPs such as Ramco will have provision to calculate the NRV for an order and enable users to prioritize the orders. Starting from the quotation stage and beyond, the NRV can be calculated on the fly and mix design can be formed based on the NRV.
Yes, some RMC ERPs handle complexities like asset leasing. They can track leased equipment and automate billing. For dump and divert scenarios, the ERP has features that can monitor leftover materials and optimize their reuse in new mixes, reducing waste and costs.