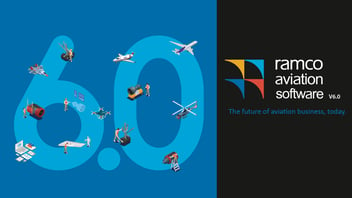
- Home
- Aviation
- Taking Off From An IT Runway Instead Of Regular Tarmac – Leveraging Ramco's Leap Methodology
Taking Off From An IT Runway Instead Of Regular Tarmac – Leveraging Ramco's Leap Methodology
Published :
Introduction to LEAN:
Lean philosophy regards anything that doesn’t add value to a process or a product or that for which the customer is not willing to pay for, as waste and should be eliminated. The lean thinking had its beginning in the early 20th century from the works of Mr. Henry Ford, who integrated an entire production process to eliminate wastes. The lean thinking was further taken to a new level by Toyota who defined the Toyota Production System.
All the while, lean thinking was finding itself confined to the manufacturing industry. It took time for industry specialists to understand the lean opportunity present in the services sector. Of this, the venture of Lean into IT products & services is a very recent development.
Usually in an organization, when the idea of implementing lean initiatives is considered, the first question that pops up is “Why Lean??” - acasual question asked by someone who doesn’t understand lean philosophy. In simple terms, “it’s just a better way of doing things”. ‘Better’, in this sentence translates to saving time and reducing cost incurred byeliminating wastes in multiple facets. The wastes as identified by the Toyota’s TaichiiOhno, were:
a) Transportation
b) Inventory
c) Motion
d) Waiting
e) Over-production
f) Over-Processing
g) Defects
The easier way to remember the 7 wastes of lean manufacturing is the mnemonic TIMWOOD. All these wastes were identified in the production or mainly in a manufacturing setup. But to identify the same for an IT services or products industry is not easy. A software deployment process, has its set standard procedures. This has been followed for many years thus indoctrinated as standards of the system. The matter of concern was the time and cost incurred in Software implementation. This was not affordable to smaller players in industries. Thus,came the idea of bringing in the Lean thinking in the implementation process. RAMCO uses LEAN IMPLEMENTATION METHODOLOGY entitled as Ramco’s LEAP methodology. LEAP methodology was designed and formulated specifically for small operators allowing them to experience and realize the benefits of comprehensive mainstream full suite Aviation solutions.
Ramco’s LEAP Methodology:
Ramco’s LEAP methodology surgically augments the basic principal of LEAN philosophy to improve the software implementation process. The 7 wastes of Lean manufacturing can be categorized as:
Over the years, there is an 8th waste that was identified – SKILLS, due to under-utilization of resources & delegating tasks with inadequate training. This waste can be eliminated by efficient training and effort tracking. Ramco follows a stringent effort tracking process.
All this enabled the reduction of the software implementation process time from 8-12 months to 3-4 months or to even 33-45 days. Using Ramco’s LEAP Methodology, Customers benefit from faster realization of the software. LEAP thinking is an asset both to Ramco and its Customers!
(Inputs by: Akhil Farook and Janeese Jacob Cherian)
All Rights Reserved. © Copyright 2024. Ramco Systems.