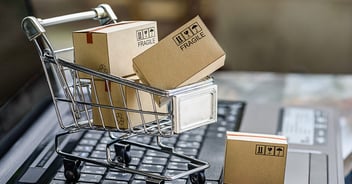
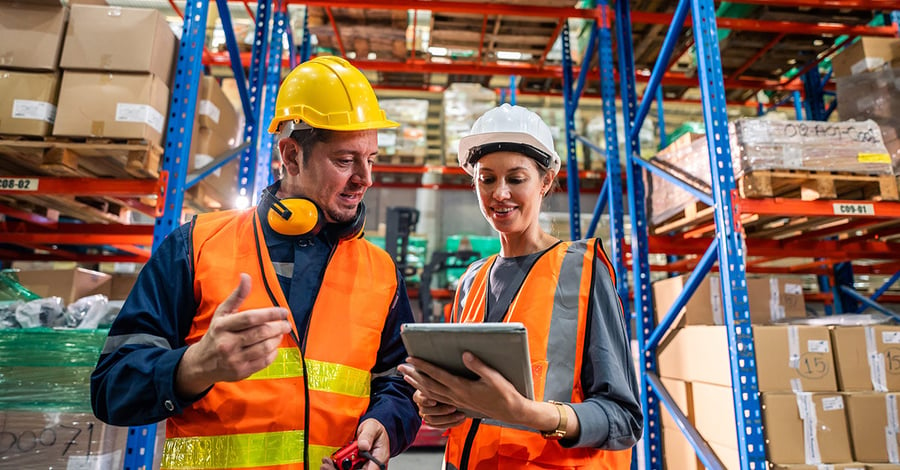
Effective warehouse space utilization is crucial for business success. By optimizing your storage space, you can reduce costs, improve efficiency, and enhance overall warehouse performance. A recent study revealed that average peak warehouse utilization was 85.6%. Almost 37% of facilities were pushed beyond 95% capacity. Significantly, 47% of respondents reported needing more warehouse space. This highlights the need to optimize warehouse space utilization.
This blog explores key metrics, factors influencing inventory, and strategies and technologies, including warehouse management systems to maximize space utilization.
Understanding Warehouse Space Utilization
Warehouse Capacity Utilization is a measure of how effectively the available space is utilized in the warehouse. This metric provides insights into the efficiency of space utilized within the warehouse and helps to identify underutilized areas and opportunities for optimization, influencing profitability and operating efficiency.
Warehouse Capacity Utilization is calculated based on Total Utilized Capacity divided by the Total Available Capacity for a given period (Period can be for Current Date Time, Week, and Month): (Total Utilized Capacity/Total Available Capacity)*100.
Warehouse management systems can be instrumental in optimizing warehouse space utilization. However, before proceeding, let’s explore the commonly used metrics to measure warehouse space utilization.
Total Utilized and Available Capacity can be calculated based on the number of bins, pallet spaces, and storage space.
- Total Utilized Capacity – Actual space occupied by the stock in the warehouse. This can be defined based on the number of bins and pallet spaces, or the number measured in square/cubic feet.
- Total Available Capacity – Total space which is available in the warehouse for storing the stock excluding inactive or damaged bins.
- Unavailable Capacity – Total space that is inactive or damaged and not available for storage
Factors Contributing to Fluctuating Inventory Levels
Fluctuating inventory levels can significantly impact a logistic service provider’s business profitability and customer satisfaction. A few factors affecting inventory levels are:
- Seasonality: Products with seasonal demand like winter clothing and holiday decorations experience significant inventory fluctuations.
- Changing customer preferences: Rapidly changing consumer preferences can lead to unexpected inventory surpluses or shortages.
- Competition: Aggressive pricing or promotional activities by competitors can impact demand and inventory requirements.
- Geopolitical Events: Political instability or conflicts can impact the economic condition of a country, affecting demand and inventory levels.
- Supply Chain Disruptions: Transportation challenges, port congestion, labor shortages, or natural disasters can disrupt the flow of inventory.
- Raw Material Availability: Shortages or price fluctuations of essential raw materials can impact production and inventory levels.
Strategies for Optimizing Warehouse Space Utilization
Below are some of the strategies for optimizing warehouse space utilization.
Inventory Management Techniques:
Slotting and Dynamic Slotting: Slotting is the process of assigning specific locations to products in a warehouse. Dynamic slotting is a more flexible approach. Product locations are changed using real-time data based on factors like demand, seasonality, inventory turnover, and storage costs. This strategy helps optimize warehouse space utilization by ensuring that frequently accessed items are stored in easily accessible locations, reducing travel time for workers and improving overall efficiency.
ABC Analysis: Categorizing inventory into A (fast-moving), B (medium-moving), and C (slow-moving) items allows for strategic placement. High-demand items are stored in easily accessible locations, while slow-moving items can be placed in less optimal areas.
Cross-docking: This technique of warehouse management systems bypasses traditional storage by directly transferring incoming goods to outgoing shipments. This significantly reduces storage time and frees up valuable warehouse space. With efficient logistics planning and coordination, warehouse efficiency and turnover can dramatically improve.
Warehouse Layout Optimization:
Vertical Storage Solutions: Helps maximize warehouse space by utilizing the height of the building. Techniques like pallet racking, shelving, cantilever racking, etc., create additional storage levels, increasing capacity without expanding the footprint. This optimization improves space efficiency and accessibility to stored items and reduces operational costs and picking times.
Mezzanine Floors: Using mezzanine floors creates additional storage space within an existing warehouse by constructing intermediate levels. This maximizes vertical space utilization without expanding the building. Ideal for slow-moving or low-density items, mezzanine floors are versatile and customizable, improving overall warehouse efficiency and capacity.
Designing Efficient Pick Paths: Minimizes travel time within the warehouse, increasing productivity and reducing labor costs. Businesses can streamline order fulfillment, improve accuracy, and free up space for additional inventory by optimizing the sequence of picking locations and using tools like pick-to-light systems. Techniques like zone picking, batch picking, and wave picking contribute to efficient pick paths.
Technology and Automation:
Warehouse Management Systems: WMS software optimizes space allocation by leveraging real-time inventory data to strategically position products. Considering factors such as product dimensions, weight, demand, and turnover rates, the Warehouse Management System facilitates efficient placement, maximizing storage capacity and minimizing wasted space. Advanced features like demand forecasting and space utilization analytics further enhance this process by predicting product movement and identifying underutilized areas, ultimately improving overall warehouse efficiency. It’s predicted by 2025, the global warehouse management system (WMS) market will be worth $4.1 billion.
Automated Storage and Retrieval Systems (AS/RS): Optimize space by utilizing vertical storage to its maximum potential. These systems employ robots to store and retrieve items from high-density racks, maximizing cubic capacity and eliminating wasted aisle space. AS/RS also improves order accuracy and reduces labor costs, indirectly contributing to space efficiency by streamlining operations.
Internet of Things (IoT): Empowers real-time inventory tracking and space management. By using sensors and RFID tags, warehouse operators gain precise visibility of product locations and quantities. This data drives efficient space allocation, reduces search times, and prevents overstocking. IoT also enables predictive analytics for optimizing storage based on demand patterns and product turnover.
Flexible Storage Solutions:
Modular Storage Units: Offer flexibility for optimizing warehouse space. These units can be easily rearranged or relocated to accommodate changing inventory levels and product sizes. They maximize space efficiency by allowing customization and adaptability within the warehouse layout.
Renting Additional Space During Peak Seasons: This strategy helps manage seasonal demand surges, avoid stockouts, and maintain customer satisfaction without compromising operational efficiency. By expanding storage capacity temporarily, companies can avoid overinvesting in permanent warehouse space and associated costs.
Partnering With Other 3PLs for Shared Storage Solutions: This collaborative approach offers a cost-effective way to optimize warehouse space. By sharing warehouse facilities, logistics service providers can reduce overhead costs, access specialized storage capabilities, and increase flexibility.
Logistics Leaders: Mastering Space with Warehouse Management Systems
A logistics giant, Visy sought to optimize its warehouse operations amid supply chain challenges. Visy achieved a fully automated warehouse by implementing the Ramco WMS software and integrating it with 28+ systems, including AGVs. This seamless integration resulted in flawless order fulfillment, reduced operational costs, and improved overall efficiency, including space optimization. The successful automation project solidified Visy's position as a leader in smart logistics solutions.
While optimizing warehouse space is crucial, it is not devoid of any challenges. You need accurate data but space constraints, product diversity, and labor requirements often hinder efforts. Technology investments like advanced WMS software and automation are a must but they can increase costs. Further, scaling strategies for future growth and evaluating ROI are crucial. While the challenges may appear overwhelming, partnering with a reliable WMS software provider can help overcome these hurdles and maximize space efficiency.
Conclusion
Optimizing warehouse space is crucial for boosting efficiency and profitability. Effective space utilization, powered by a robust warehouse management system, cuts costs by reducing storage, labor, and equipment needs. It speeds up order fulfillment, boosts customer satisfaction, and enhances safety. Ultimately, it contributes to increased revenue by maximizing output and reducing waste.
Is your warehouse working at its full potential? Assess your space utilization now! Uncover hidden costs and boost efficiency. Optimize for growth and profitability with WMS software. Contact Ramco for further assistance on warehouse management systems or consultation.
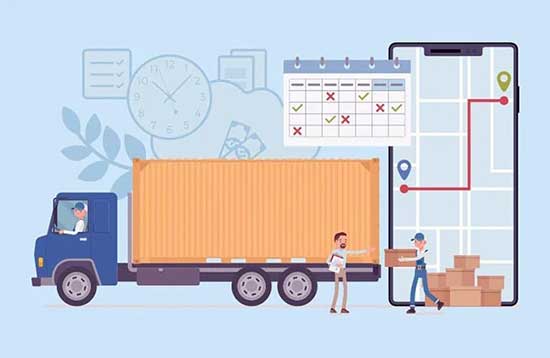