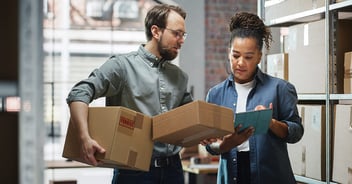
Top 5 Methods to Improve Warehouse Picking Efficiency
Published :
Every warehouse manager understands the value of timely order fulfilment. Order choosing is a dynamic process that changes by the day, hour, and minute. There's always room for improvement, no matter how efficient or effective a warehouse manager attempts to be.
Order picking is the most labor-intensive element of any warehouse operation, and this is no secret in the warehousing sector. According to studies, the selecting process accounts for around 55 percent of your warehouse's labor burden. Customer service is harmed, overhead expenses rise, and your supply chain is weakened due to poor selecting performance. Improving your order-picking approach will, of course, increase your profits. Before investing in any kind of Warehouse Management system, we should understand the following concepts that can elevate picking efficiency.
No two warehouses are alike, but also true that many warehouses face the same issues. The most pressing issue for which you'd prefer a practical solution is how to increase your pick rate. Picking improvement does not come with a miraculous pill or bullet. It's more of a succession of tiny measures that you can take to achieve success.
Since order picking takes up more than half of your staff's time, cutting down on travel time is a no-brainer. Keeping your high-volume stock close to your throughput end is critical to cutting trip time. However, there is more you can do to improve your travel efficiency. Consider setting up your warehouse so that you may pick from both sides of the racks. Slow-moving things can be stored deep inside your racks, while high-volume items can be stored towards the front edges. Picking up many orders in one trip also tremendously reduces travel time. Investing in material-handling equipment that reduces travel time, curbs worker strain, and allows workers to work safely without accidents is also a good idea.
Hot zones or hit zones are designated storage areas for fast-moving goods. This broadens the 80/20 rule and makes it more adaptable in response to peak demands about goods and consumer requests. Seasonal goods that correspond to weather trends are excellent candidates for your hot zone. Like other high-priority products, Hot zone items should be placed at locations that require minimal travel time. They should also sit in locations with little traffic so that material-handling equipment such as carts, dollies, and pallet trucks do not collide.
The A-B-C technique is a smart order selection efficiency solution. This entails determining the demand for each SKU product and the throughput time. A-priority SKU products, for example, are fast-moving, high-demand items. B-priority SKUs are assigned to products that are in high demand. A C-priority is for low-demand and slow-moving items.
After you've created your high, medium, and low priority SKU groupings, arrange them in your warehouse so that each group has its own space. A-priorities should be the easiest to reach and take the least amount of time. Mid-warehouse locations should be B-priorities. C-priority SKU items can be stored separately from your throughput tail section at the farthest distance.
Congested and packed warehouses are inefficient. Layouts with too much space between racks, aisles that are too long to travel through, and inadequate equipment staging areas are all examples. The layout of your warehouse influences order picking efficiency. Take a look at your material-handling equipment to ensure enough room to pass, turn, and load without colliding with racks or other order pickers. When it comes to ordering selection, having the correct size and rating for your material-handling components makes all the difference. Your warehouse layout and equipment should work together rather than against one other.
With the correct material-handling equipment, there's little doubt that your order picking efficiency will not skyrocket. You'll save time choosing orders with high-quality equipment like hand trucks, dollies, and carts. You'll also be able to work more safely. As a result, there is reduced downtime due to accidents. Containers and bins help improve order picking efficiency. Whether a hot zone A-priority or a C-SKU, you'll have everything in its designated location. Don't underestimate the importance of shifting heavy items for picking efficiency.
Due to the order count and SKU count, this value can be improved by adjusting the constraints applied to the process. A redesigned picking cart could result in a 50 percent increase in productivity. Path optimization might be used in the putting away process, which could be moved from waves to batch or cluster-based putting away. A Warehouse Management System that can help incorporate and track all these parameters in the warehouse will be a game changer.
All Rights Reserved. © Copyright 2024. Ramco Systems.