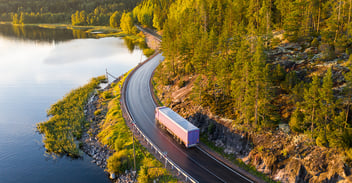
From Cross-Dock Chaos to Transport Triumph: How to Optimize Labor & Maximize Savings
Published :
For years, transport owners have been burdened with the inefficiencies of transitioning from cross-docking operations to execution transport. This changeover, while crucial for improving service and delivery times, often introduces labor waste, duplicated administrative efforts, and a drain on the bottom line. The core issue lies in managing this shift without the right tools or strategies in place, resulting in operational bottlenecks that diminish the potential gains.
Cross-docking is a more straightforward system that prioritizes quick movement of goods, but as businesses scale and demand higher execution efficiency, transport owners are forced into a complex juggling act. Without clear oversight, labor hours are wasted on manual tasks, and administrative teams often find themselves duplicating efforts just to keep up. For many transport businesses, this situation creates a vicious cycle where unnecessary labor costs eat into profitability.
One of the oldest solutions to inefficiency is the classic "management by walking around." Walking the floor daily gives transport owners a ground-level view of operations, but this only scratches the surface of what’s really going on. While it may help identify minor bottlenecks, it doesn’t provide a clear, data-driven view of the bigger picture.
Owners and managers may spot operational missteps, but the repetitive nature of manual oversight isn’t sustainable. It becomes impossible to accurately track waste and inefficiency without visibility across the entire operation.
The real solution lies in investing in tools that provide a comprehensive, macro-level view of the entire operation. Modern transport management systems (TMS) offer a bird’s-eye perspective of daily tasks, from shipment execution to route planning, workforce management, and resource allocation. These systems can pinpoint where time, labor, and money are being wasted, allowing for more strategic decision-making.
The ability to track key performance indicators (KPIs) across all touchpoints in the transport process can turn guesswork into actionable insights. A data-driven approach not only reduces the manual, repetitive work but also empowers businesses to make smarter, faster adjustments to their operations.
The shift from cross-dock to execution transport doesn’t have to be a source of frustration. With the right tools in place, transport owners can reduce waste, eliminate duplicated administration, and focus on what really matters—delivering value to their customers.
In the end, managing the transition efficiently is about understanding the data, streamlining processes, and ensuring that every operational move enhances profitability rather than diminishes it. Investing in technology today can prevent years of operational pain and give transport businesses the edge they need to thrive in a competitive landscape.
Ramco has delivered several tangible results for transport owners transitioning from cross-dock to execution transport. Here are some key examples:
Ramco’s Transport Management System (TMS) has helped clients cut down manual route planning, which often leads to inefficiencies. For instance, a large logistics provider was able to automate route optimization, resulting in a reduction in fuel costs and fewer driver hours, directly lowering operational expenses.
Ramco’s platform integrates real-time tracking, providing a macro-level view of all ongoing operations. One client reported an improvement in delivery time and a decrease in customer service inquiries by giving customers live updates on their shipments, reducing administrative burdens tied to manual tracking.
Ramco introduced a paperless freight documentation process, eliminating the need for manual data entry. This change saved a client hours per week in administrative tasks, which previously involved duplicated effort across teams. It also reduced errors, improving billing accuracy by.
By integrating predictive maintenance tools within their TMS, Ramco helped a transport fleet reduce unexpected vehicle downtime. This not only saved on repair costs but also optimized fleet usage, increasing overall productivity and reducing labor wasted on unplanned disruptions.
Ramco enabled a logistics company to scale its workforce more effectively by forecasting labor needs based on historical data. This approach led to better labor distribution during peak times and reduced idle labor hours, ultimately saving the company thousands in unnecessary labor costs each month.
Ramco’s TMS offers customizable dashboards that provide key performance insights at a glance. One client reported a increase in overall efficiency by using these dashboards to quickly identify and address operational bottlenecks, without needing to micromanage each process.
These examples showcase how Ramco’s TMS and other digital solutions help transport owners streamline their transition from cross-dock operations to a more efficient, data-driven execution transport model, resulting in tangible cost savings and productivity gains. Stay safe as we enter Peak Season.
All Rights Reserved. © Copyright 2024. Ramco Systems.