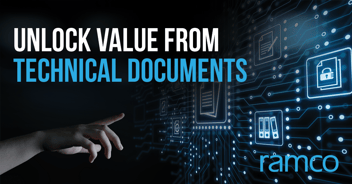
5 Steps To Unlock Value In Engine Maintenance Process
Published :
Aircraft engine maintenance service providers recognize that their operations and maintenance processes are unique and complex when compared to hangar, line, and component maintenance processes. If you are a part of an aircraft engine maintenance system/organization and find yourself nodding to the points mentioned below that have caused inconvenience, then you are not alone.
So, read on to see the 5 potential areas that will simplify and also add value to this entire process.
The engineering and technical records department put in loads of effort and time to process the OEM’s technical documents (such as Service Bulletin and Information letters) and manuals (ESM, SPM, etc). This can range from occasional induction of a new set of technical documentation for a particular engine type to continuous and incremental revisions to these documents. As the formats of these documents vary, so does the effort required to process them. The XML/SGML-based document formats are efficient to ingest and render the output in HTML for an interactive experience to the users (refer to Fig. 1). PDF-based documents need extensive efforts to process.
Fig. 1: XML/SGML-based documents processing
Having the right content management system that is well integrated with the core M&E system increases the operational efficiencies, by reducing the time and effort required to process the technical contents. The table below lists the capabilities that a content management system must have that will help the organization gain efficiencies in this process. Engine MRO looking to embrace digital transformation will be challenged downstream unless this area is completely equipped with robust and intelligent system capabilities.
Capability | Efficiencies gained through... |
Ability to process the PDF-based technical documents |
|
Ability to process XML/SGML-based technical documents |
|
Direct Electronic Data Interchange (EDI) capabilities with OEM sites |
|
Digital enablers |
|
New task cards related to SB/AD (Service Bulletins / Airworthiness Directive), which does not have a baseline reference, need user intervention to collect standard manhours from external sources and applying the MRO factor to arrive at the planned manhours.
Part lists are also compared with the existing part library and new part number which needs to be created are listed separately. This creation process is semi-automated as it requires additional data both from intelligent defaults and user specified.
(If you want to know more about this, you can read a detailed blog on this here.)
Aviation maintenance processes typically generate a wealth of data pertaining to the aircraft engine defects, parts consumed, labor hours, elapsed time to carry out the repair and overhaul procedure, etc. Accumulated over time, this data can be utilized to gain insights through AI/ML, automate the core operations and ultimately gain an edge over the competition. Legacy applications may have the advantage of accessing the rich data accumulated but their ability to derive advantage is limited due to the existence of data silos and lack of advanced capabilities to harness the data.
The following table indicates the areas that can leverage data and AI/ML digital capabilities to provide key business benefits.
Core Process | Potential Automation Areas |
Workscope planning & estimation |
|
Production planning & scheduling |
|
Supply chain management |
|
Empowering the shop floor mechanics with mobile-based work execution tools (refer to Fig. 2) is a proven way to reduce the non-production hours and enhance productivity. This is primarily due to a significant reduction in physical movements that are needed for accessing the required support. Mobile-based work execution enables the mechanic to book time, report findings and record measurements, request parts and tools, and access the technical documents from the place of work. With the required regulatory approvals that were easily acquired through mobile apps, task and work compliance can be complied with through a digital e-signoff.
and work compliance can be complied with through a digital e-signoff.
Fig. 2: Mobility-based shop floor execution
Mechanics can raise technical requests, collaborate with the technical teams through voice and video chat in real-time to get feedback or advice on resolution. Well-authored task and process sheets can intuitively guide the mechanics to report their observations, measurements, and tolerances at the appropriate sections. The reported data are checked with the standard or OEM reference to assist the mechanics to take decisions. This data is even stored and leveraged for analytics and ML-based recommendations.
The seamless flow of data between the ecosystem partners (refer to Fig. 3) is essential for augmenting operational efficiency. The aircraft maintenance process involves routing the engine sub-assemblies to external repair, exchanges, and purchase of the parts with suppliers. By leveraging aviation industry protocols (Spec 2000), the processing time and quality of data exchange can be significantly improved. Processing real-time data on shipments improve marshalling and production control efficiencies.
Fig. 3: Seamless flow of data between ecosystem partners
Enabling a robust EDI connection with customer systems provides an MRO aviation with the dual advantage of boosting efficiency and also improving the delivery of value to the customers. The possible avenues of the EDI exchanges are work scope, configuration snapshots, additional work requests, and out-of-scope approvals. These information exchanges can also be achieved by enabling the customer portal. Pivoting all the communications within the system framework enables the comprehensive data source for business and KPI measurements.
Also Read: Reliability Centered Maintenance (RCM) in Aircraft Maintenance
Having an integrated system that assures paperless operations ensures that the data collected are entered at the point of source. Key KPIs related to TAT, quality, cost, resource utilization, and warranties are computed dynamically without any need for manual consolidation and preparation. This makes way for a transparent and timely availability of insights for better decision-making.
Faced with the twin objectives of operational efficiency and reducing costs, engine MROs need to embrace an integrated platform and digital technologies to future-proof their business. MROs need to rethink their improvement projects and should instead consider these 5 steps in their digital adoption strategies to unlock the maximum value.
This blog is a part of the Digital Aviation MRO blog series. You can check out the previous blog in this series here and here. For any further clarifications, you can reach out to us at contact@ramco.com
All Rights Reserved. © Copyright 2024. Ramco Systems.