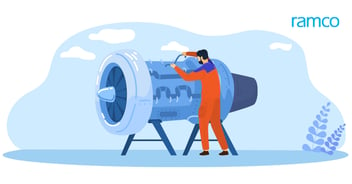
3 metrics to get right in your rotable inventory ecosystem
Published :
The ongoing pandemic dramatically cut the flying hours resulting in lower requirement of parts. Organizations utilized swaps from the parked aircrafts and availability of used serviceable materials to reduce the cash burn. Organizations across the world are rebuilding their rotable inventory management strategies especially with focus on the cost optimization and agility to adopt to changing business models. Incorporating a digital backbone enables organizations to leverage the data and tools to unlock value through digitization and automation.
Rotable inventory management in many organizations still grapples with decoupled systems within organization, decentralized data, manual processing of paper trails, non-standardized adopters to exchange data outside organization, no real-time visibility of key KPIs. Any company that orchestrates an ecosystem will need to address not only business KPIs but also technical considerations to measure and improve the KPIs.
Establishing the contract with 3rd party customer or internal material management team is first step to improve the service level fulfilment. The detailed terms and conditions on parts in scope, agreed service levels for various types of demand AOG, routine etc, INCO terms or handover points, penalty clauses are essential to initiate, monitor and control the KPI. Refer Fig-1
Fig-1: Monitoring of SLA on real-time
Considerable time is spent on processing the part demand due to disparate systems or manual involvement involved in registering the demand and cross-referencing with the contractual scope. Enabling the customers with the options of placing part demand through multiple channels (customer portal, API based plugins for processing the demand through EDI channels) provide the end-to-end visibility of the demand with no manual intervention.
The demands received through various channels can be screened with the respective contracts and any out-of-scope demands are flagged to manual attention for possible upsell through exchanges or loans. Demands flagged as in scope are further automated to pick the right serial/lot # from the rotable inventory based on the customer contracted technical requirements on release certificates, component life, component conditions like PMA, new, USM, mod/version #. This significantly reduces the picking time thereby improving the service levels and reducing noncompliance returns from maintenance.
Similar to metric 1, the prerequisite to improve DMC is to establish the 3rd party service providers or internal shops. The detailed terms and conditions on contracted part # capability listing of the supplier/ shops along with the agreed TAT, pricing, penalty, exclusions in any for essential drive downstream repair order automation. Initiating terms related to supplier warranty helps for automated tracking and claim processing.
Having the contracted terms with the 3rd party customer or maintenance departments on return KPI and tracking it with penalty clause helps in accelerating the return of the item to base.
Considerable time is spent to process the unserviceable items receipt, analysing the work scope, identifying the repair options due to manual involvement involved during these stages. Smart automation based on the customer and vendor contracts can automate at least 80% of repairs. Process can intelligently automate the decision to repair or hold (due to warrant or float, poor reliability) and add the required work scope from maintenance program. Leveraging AI\ML best supplier can be recommender-based location work scope, TAT, and cost requirements Refer Fig-2
Fig-2: Automation of Repair order processing
Establishing an API based data transfer for entire repair order process through EDI data exchange helps in improved data accuracy and order processing time. It is essential to track repair cost split between actual repair/ overhaul/ test cost or logistics cost or mod cost distinctively during the quote process to enable analysis on the overall DMC improvements, cost deviation and escalations.
It starts with the foundational aspect of managing the interchangeability between the parts and managing the key interdependencies of conditional, supersedes and Next Higher Assembly (NHA). Rotable inventory planning needs to be carried out at various levels starting with the whole enterprise, for specific pool location, for a specific customer, aircraft type or even for specific part or ATA group. On an ad-hoc basis the analysis needs to be executed during SLA failure cases or scrap disposals events to take immediate corrective action.
Rotable Inventory optimization needs to consider all the key parameters like schedule demand, MTBUR, purchase and repair TAT, Scrap rate. After processing the overall demands, supply position, SLA, reliability data and leveraging AL/ML based algorithms, you should be able to get the optimum rotable inventory requirements and recommended action (improve reliability, reduce TAT, purchase, etc.) to take. Refer Fig-3
Fig-3: Leveraging ML based recommendation for Rotable Inventory optimization
Time to manage Rotable inventory digitally
Faced with the twin objectives of reducing costs and being agile, organizations need to embrace an integrated platform and digital technologies to future-proof their rotable inventory management practices. With this foundation in place, organizations have the potential to achieve the 10% improvement in Service levels, 15% reduction in DMC and 5% reduction in rotable Inventory.
This blog is a part of the Digital Aviation MRO blog series. You can check out the previous blog in this series here. You will also find more relevant information from our recent webinar on Rotable Inventory management, which can be accessed here.
All Rights Reserved. © Copyright 2024. Ramco Systems.