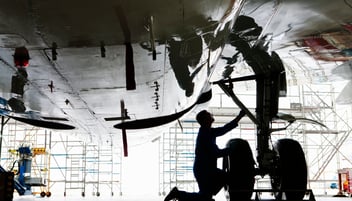
“When you’re working on a plane, fix it to the degree you would if the most important person in your life is flying on it next.”
This is one of the quotes which always remain in the minds of aircraft maintenance engineers and mechanics while performing daily maintenance tasks. Aircraft maintenance is perhaps one of the most important elements of aviation industry, constituting around 25% of the operating cost annually. The pressure of delivering on-time maintenance task is only going to increase in near future as the air-traffic continues to grow exponentially with improved economic condition and subsequently will lead to increased demand of aircraft utilization. In such situations, clearly, aircraft mechanics and technicians emerge out to be true heroes. Mechanics muddle up throughout the day putting oil in engines, reading lights, checking tire pressure and hundreds of other things as part of their day-to-day tasks. The aircraft technicians and mechanics spend a major portion of the day using a wide variety of hand tools to accomplish daily maintenance tasks. Without the aircraft tools, even these heroes are helpless.
Consider a situation where in an Aircraft arrives in the ramp and needs a quick fix within a stipulated time. Mechanics work round the clock and button up the aircraft after extensive work under tight time constraints. To their satisfaction, these mechanics finally watch the aircraft taxi out for its first flight in the morning. A major twist in the plot comes when these heroes’ turn out to be “accidental” villains. Just when the aircraft was taxing out of the hangar, one of the mechanics glances into his tool box and wonders where the screwdriver is! What a nightmarish situation and every mechanic try to avoid this one in particular. Leaving a tool in an aircraft or engine is not just an inconvenience, it is a safety risk. Foreign Objects are a major cause of aircraft damage and unscheduled maintenance. Damage can result in minor repairs or catastrophic events.
An interesting survey was carried out during Aviation Week's MRO Europe Conference in 2013. When the audience were asked, “how concerned are you about the effectiveness of your tool control process,” on a scale of 0-10, the average answer was a slightly concerning 6.15. However, note that only 8% selected a 0 or 1 (the lowest concern) versus 22% who chose 10 (the highest). Delving into those extremes, 50% of the “10s” came from airline carriers' line-maintenance/operations support, versus 37.5% from MROs and 12.5% from OEM. It is clear that Tool Management is becoming the buzz word in the aviation industry as aircraft maintenance providers look to leaner the process alongside greater accountability. Tools are not only used in maintenance facilities but are also used in on-field maintenance activities, for instances, rotor wing operators who need to maintain ‘on-the-go’ tool kits because of the diversity in the aircraft operations ranging from offshore oil exploration to firefighting from cities to jungles. Another point which came out during the survey was the obstacles in adopting tool control practices and they were capital cost, internal resistance and right technology. The cost drivers for poor tool control are lost productivity, labor dedicated to finding lost tools, operational shutdown or schedule disruption, disassembly or rework to locate a lost tool, and replacing tools.
The cost drivers can be effectively controlled by implementing effective tool management strategies. Having a full audit trail of equipment and tools used, plus calibration and inspection, creates a much more organized and highly efficient working environment. Automated tool management system helps to control these cost drivers and help alleviate the pain of tool control. The primary objective of these tool management systems is to closely track tools withdrawn from the inventory. The tool management software helps notify tools administrator about replenishing tools inventory and help him make understand the usage pattern of tools based on daily consumption. But there’s another critical objective in the airline industry, where it’s equally important to know what’s being returned to the tool crib at the end of each shift. A wayward reamer or countersink left behind in an airplane engine compartment can potentially cause thousands of dollars in damage or even engine failure. The situation is even more critical and highly regulated for Part 145 Repair Stations.
Ramco Systems brings together sophisticated Facility Management business module in their M&E Software which provides comprehensive and automated electronic tool controllable system. The benefit of automated Tool Tracking System helps improve maintenance operations by:
- Single System to track tools and maintain real time inventory of the tools. This saves mechanic’s time looking for maintenance tools across hangars, apron locations and stores.
- Technicians can gain access to maintenance tools against their assigned authorized employee ID with no additional manual data entry. The tools return process is just as simple and fast thus reducing Foreign Object Damage (FOD) risk.
- Tool calibration schedule is effectively managed as it is a very important process since improperly calibrated tools and measurement devices don't do what you expect them to do. For instance, a click-type torque wrench whose spring is `out of spec' can end up delivering less torque per turn; resulting in nuts that aren't on as tight as the manufacturer requires. Similarly, a tire gauge that isn't reading properly may result in increased aircraft tire wear due to under-inflation.
FOD reduction, less time searching for tools, better inventory control and obtaining metrics on maintenance tasks/repair flow all leads to a more efficient and cost-effective operation.
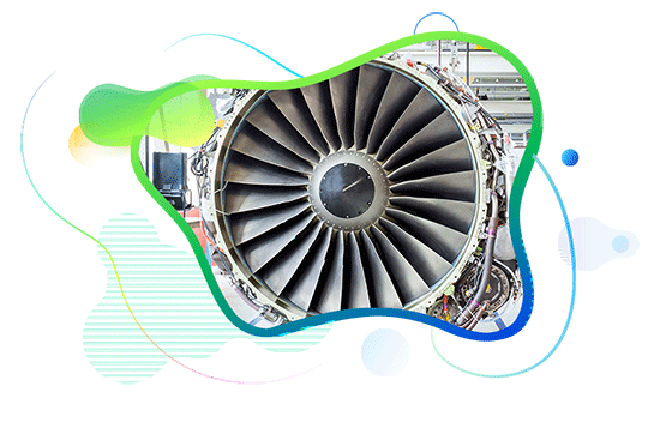